W dzisiejszym świecie przemysłowym, cięcie metalu jest nie tylko kluczowym procesem, ale również fundamentem innowacji i efektywności w produkcji oraz konstrukcji. Poznanie różnych metod cięcia metalu jest istotne, ponieważ każda z nich oferuje unikalne zalety i spełnia różne wymagania techniczne i ekonomiczne. W tym artykule skupimy się na głębszym zrozumieniu tych technik, porównując je z nowoczesną metodą cięcia strumieniem wody, znaną jako waterjet.
Spis treści:
Cięcie Plazmowe
Cięcie plazmowe, wykorzystujące naładowane elektrycznie, supergorące gazy, jest metodą, która zrewolucjonizowała przemysł cięcia metalu. Ta technika, polegająca na tworzeniu plazmy, czyli jonizowanego gazu zdolnego do przewodzenia prądu, umożliwia szybkie i efektywne przecinanie nawet grubych płyt metalowych. Jest to szczególnie ważne w przemyśle, gdzie czas i wydajność są kluczowe.
Jedną z głównych zalet cięcia plazmowego jest jego szybkość i efektywność, co jest niezwykle cenne w szybkich cyklach produkcyjnych. Dodatkowo, jest to stosunkowo niedroga metoda w porównaniu z innymi technikami cięcia, co czyni ją atrakcyjną dla wielu zastosowań przemysłowych. Plazma radzi sobie również z cięciem metalów o znacznej grubości, co jest trudne do osiągnięcia dla innych metod, takich jak cięcie laserowe.
Jednakże, cięcie plazmowe ma również swoje ograniczenia. Generowanie wysokiej temperatury prowadzi do powstania strefy wpływu ciepła (HAZ), co może powodować deformacje i osłabienie strukturalne materiału, szczególnie w przypadku skomplikowanych geometrii. Wysoka temperatura może również powodować topienie i zniekształcenia w miejscach cięcia, co jest szczególnie problematyczne przy precyzyjnych detalach. Ponadto, proces cięcia plazmowego może generować szkodliwe gazy, co stanowi wyzwanie dla bezpieczeństwa i ochrony środowiska.
Mimo tych ograniczeń, cięcie plazmowe pozostaje popularną i cenioną metodą w przemyśle, oferującą unikalną kombinację szybkości, efektywności i wszechstronności. Jego zdolność do radzenia sobie z różnorodnymi rodzajami i grubościami metalu sprawia, że jest to niezastąpiona technika w wielu zastosowaniach przemysłowych.
Cięcie Gazowe (Oxy-fuel)
Cięcie gazowe, często określane jako cięcie tlenowo-paliwowe, jest jedną z bardziej tradycyjnych metod cięcia metalu. Ta technika, polegająca na wykorzystaniu ognia do wycinania kształtów w metalach, ma swoje korzenie w początkach przemysłu metalurgicznego. Mimo że jest uważana za bardziej prymitywną niż nowoczesne metody, takie jak cięcie plazmowe, nadal odgrywa ważną rolę w wielu zastosowaniach przemysłowych.
Jedną z głównych zalet cięcia gazowego jest jego zdolność do przecinania bardzo grubych płyt metalowych, co często przewyższa możliwości cięcia plazmowego. Ta metoda jest szczególnie przydatna w przypadku ciężkich prac konstrukcyjnych, gdzie wymagane są duże i grube elementy metalowe.
Jednakże, cięcie gazowe ma swoje ograniczenia. Przede wszystkim, nie jest odpowiednie do cięcia stali nierdzewnej i metali nieżelaznych, co ogranicza jego zastosowanie w niektórych branżach przemysłowych. Podobnie jak w przypadku cięcia plazmowego, cięcie gazowe generuje strefę wpływu ciepła, co może prowadzić do deformacji i osłabienia strukturalnego materiału, szczególnie w przypadku skomplikowanych geometrii.
Ponadto, cięcie gazowe wymaga znacznej umiejętności i doświadczenia operatora, aby zapewnić precyzję i bezpieczeństwo procesu. Jest to metoda, która wymaga ostrożności, ze względu na otwarty ogień i wysokie temperatury zaangażowane w proces.
Mimo tych wyzwań, cięcie gazowe pozostaje ważną metodą w przemyśle, szczególnie w sytuacjach, gdzie inne metody cięcia są niewystarczające lub nieekonomiczne. Jego zdolność do radzenia sobie z grubymi metalami i prostota sprzętu sprawiają, że jest to metoda ceniona w wielu zastosowaniach, zwłaszcza w ciężkim przemyśle i budownictwie.
Cięcie Laserowe
Cięcie laserowe, wykorzystujące skoncentrowaną wiązkę laserową wspomaganą gazem, stanowi jeden z najbardziej zaawansowanych i precyzyjnych metod cięcia materiałów, w tym metalu. Ta nowoczesna technologia, łącząca precyzję z efektywnością, zrewolucjonizowała wiele aspektów produkcji przemysłowej, oferując niezrównaną dokładność i czystość cięcia.
Jedną z głównych zalet cięcia laserowego jest jego wyjątkowa precyzja. W porównaniu do cięcia plazmowego i gazowego, laser zapewnia znacznie cieńszą linię cięcia, co pozwala na tworzenie bardziej skomplikowanych i szczegółowych kształtów. Dodatkowo, cięcie laserowe charakteryzuje się mniejszą strefą wpływu ciepła (HAZ), co minimalizuje ryzyko deformacji i osłabienia strukturalnego materiału.
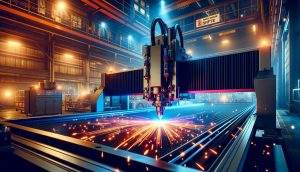
Cięcie laserowe jest idealne do pracy z cienkimi blachami metalowymi, gdzie jego precyzja i zdolność do szybkiego przecinania są szczególnie cenne. Ta metoda jest szeroko stosowana w przemyśle motoryzacyjnym, lotniczym, a także w produkcji precyzyjnych komponentów.
Jednakże, cięcie laserowe ma również swoje ograniczenia. Jednym z nich jest trudność w cięciu metalów odblaskowych, takich jak aluminium i miedź. Odbijająca powierzchnia tych materiałów może zakłócać wiązkę laserową, co utrudnia efektywne cięcie. Ponadto, mimo mniejszej strefy wpływu ciepła w porównaniu do innych metod, cięcie laserowe nadal może generować wystarczająco dużo ciepła, aby powodować zniekształcenia, szczególnie w przypadku cieńszych materiałów.
Mimo tych wyzwań, cięcie laserowe pozostaje jedną z najbardziej pożądanych metod cięcia w przemyśle, oferując kombinację precyzji, efektywności i wszechstronności. Jego zdolność do precyzyjnego cięcia różnorodnych materiałów sprawia, że jest to niezastąpiona technologia w wielu zastosowaniach, od produkcji wysokospecjalizowanych części po tworzenie złożonych wzorów i detali.
Wycinanie Mechaniczne (Punching)
Wycinanie mechaniczne, wykorzystujące zestaw stempla i matrycy, jest metodą cięcia metalu głęboko zakorzenioną w tradycyjnych procesach produkcyjnych. Ta technika, znana ze swojej efektywności i niezawodności, jest szczególnie ceniona w masowej produkcji, gdzie konieczne jest szybkie i powtarzalne cięcie dużych ilości materiału.
Jedną z kluczowych zalet wycinania mechanicznego jest brak strefy wpływu ciepła (HAZ). Ponieważ proces ten nie wykorzystuje wysokich temperatur, nie ma ryzyka deformacji czy osłabienia materiału z powodu ciepła, co jest typowe dla metod takich jak cięcie plazmowe czy laserowe. To sprawia, że wycinanie mechaniczne jest idealne do zastosowań, gdzie integralność strukturalna i wymiary części są krytyczne.
Dodatkowo, wycinanie mechaniczne zapewnia konsekwentne wymiary części, co jest niezbędne w produkcji seryjnej. Precyzja i powtarzalność tej metody są kluczowe dla branż, które wymagają wysokiej jakości i jednorodności produktów, takich jak przemysł motoryzacyjny czy elektroniczny.
Jednakże, wycinanie mechaniczne ma również swoje ograniczenia. Jednym z nich jest potencjalne zniekształcenie powierzchni cięcia. Siła stosowana przez stempel i matrycę może powodować odkształcenia na krawędziach ciętego materiału, co może być problematyczne w przypadku precyzyjnych aplikacji. Ponadto, metoda ta ma ograniczenia w cięciu twardych metali. Twardsze materiały wymagają większej siły i mogą prowadzić do szybszego zużycia narzędzi, co zwiększa koszty i zmniejsza efektywność procesu.
Mimo tych wyzwań, wycinanie mechaniczne pozostaje ważną metodą w przemyśle, szczególnie w aplikacjach, gdzie szybkość, powtarzalność i brak wpływu ciepła są kluczowe. Jego zdolność do efektywnego przetwarzania dużych ilości materiału w krótkim czasie sprawia, że jest to niezastąpiona technologia w wielu zastosowaniach produkcyjnych.
Cięcie EDM (Electrical Discharge Machining)
Cięcie EDM (Electrical Discharge Machining), wykorzystujące naładowany elektrycznie drut przeciągany przez materiał, jest jedną z najbardziej zaawansowanych technik w dziedzinie obróbki metali. Ta metoda, znana z wyjątkowej precyzji i zdolności do radzenia sobie z trudnymi materiałami, jest uważana za rozwiązanie premium w przemyśle.
Jedną z głównych cech cięcia EDM jest jego precyzja. Technika ta pozwala na tworzenie skomplikowanych kształtów i wzorów z niezwykłą dokładnością, co jest trudne do osiągnięcia przy użyciu tradycyjnych metod cięcia. Dzięki kontroli elektrycznego wyładowania, cięcie EDM może przecinać materiały z tolerancjami mierzonymi w mikrometrach, co jest niezbędne w wysoko specjalistycznych aplikacjach, takich jak produkcja precyzyjnych narzędzi, form czy komponentów w lotnictwie i medycynie.
Cięcie EDM jest również idealne do pracy z grubymi metalami i twardymi materiałami. W przeciwieństwie do cięcia laserowego czy plazmowego, które mogą mieć trudności z przecinaniem bardzo twardych lub grubych materiałów, cięcie EDM radzi sobie z tymi wyzwaniami bez problemu. Jest to możliwe dzięki unikalnemu procesowi, w którym materiał jest usuwany przez kontrolowane wyładowania elektryczne, eliminując potrzebę stosowania dużej siły mechanicznej.
Jednakże, cięcie EDM jest procesem wolniejszym niż inne metody, takie jak cięcie wodą (waterjet) czy laserowe. Wymaga to większej ilości czasu na przetworzenie tej samej ilości materiału, co może być czynnikiem ograniczającym w szybkich cyklach produkcyjnych. Ponadto, ze względu na złożoność i koszty sprzętu, cięcie EDM jest zazwyczaj droższe niż inne metody cięcia.
Mimo tych ograniczeń, cięcie EDM pozostaje kluczową technologią w wielu branżach, gdzie precyzja i zdolność do pracy z trudnymi materiałami są bardziej cenione niż szybkość produkcji. Jego unikalna zdolność do tworzenia skomplikowanych i precyzyjnych kształtów w twardych materiałach sprawia, że jest to niezastąpiona metoda w specjalistycznych zastosowaniach.
Frezowanie
Frezowanie, będące procesem mechanicznego usuwania materiału, jest jedną z fundamentalnych metod obróbki w przemyśle. Ta technika polega na kształtowaniu pożądanej części poprzez stopniowe usuwanie warstw materiału za pomocą narzędzia tnącego, zwanego frezem. Frezowanie jest szczególnie cenione za swoją wszechstronność i zdolność do tworzenia skomplikowanych geometrii.
Jedną z głównych zalet frezowania jest jego zdolność do tworzenia ślepych otworów, kieszeni frezowanych i innych złożonych kształtów, które są trudne lub niemożliwe do wykonania przy użyciu innych metod, takich jak cięcie wodą. Ta elastyczność sprawia, że frezowanie jest niezastąpione w produkcji części o skomplikowanych kształtach, wymagających precyzyjnych tolerancji i gładkich wykończeń powierzchni.
Jednakże, frezowanie jest procesem, który generalnie jest wolniejszy i droższy niż cięcie wodą. Wymaga to większej ilości czasu na obróbkę tej samej ilości materiału, co może być czynnikiem ograniczającym w szybkich cyklach produkcyjnych. Ponadto, koszty związane z narzędziami tnącymi, ich zużyciem oraz koniecznością ich częstej wymiany mogą zwiększać ogólne koszty produkcji.
Mimo tych wyzwań, frezowanie pozostaje kluczową metodą w przemyśle, szczególnie w aplikacjach wymagających wysokiej precyzji i skomplikowanych kształtów. Jego zdolność do tworzenia precyzyjnych detali, które są trudne do osiągnięcia za pomocą innych metod, sprawia, że jest to niezastąpiona technika w wielu specjalistycznych zastosowaniach, takich jak produkcja narzędzi, form czy skomplikowanych komponentów maszyn.
Cięcie Strumieniem Wody (Waterjet)
Cięcie strumieniem wody, znane również jako waterjet, jest jedną z najbardziej wszechstronnych technik cięcia stosowanych w przemyśle. Ta metoda wykorzystuje wysokociśnieniowy strumień wody, często wzbogacony ścierniwem, do przecinania różnorodnych materiałów. Jedną z kluczowych zalet cięcia strumieniem wody jest brak wpływu ciepła na materiał, co eliminuje strefę wpływu ciepła (HAZ) i związane z nią problemy, takie jak deformacje czy osłabienie strukturalne.
Cięcie strumieniem wody charakteryzuje się wysoką dokładnością, często przewyższającą cięcie laserowe, szczególnie w przypadku materiałów o grubości powyżej 3/8 cala. Ta precyzja, w połączeniu z brakiem wpływu ciepła, sprawia, że jest to idealna metoda do cięcia szerokiej gamy materiałów, od stali, metali kolorowych po tworzywa sztuczne i ceramikę.
Jedną z wyjątkowych zalet cięcia strumieniem wody jest jego zdolność do przecinania bardzo grubych materiałów, nawet o grubości ponad jednej stopy. Ta cecha sprawia, że waterjet jest niezastąpiony w aplikacjach, gdzie inne metody cięcia, takie jak laserowe czy plazmowe, mogą być niewystarczające.
Ponadto, cięcie strumieniem wody jest idealne do pracy z bardzo cienkimi blachami. W przeciwieństwie do metod termicznych, które mogą powodować zniekształcenia lub zmiany strukturalne w cienkich materiałach, cięcie waterjetem zachowuje integralność materiału, umożliwiając precyzyjne cięcie nawet najdelikatniejszych blach.
Mimo tych zalet, cięcie strumieniem wody może być kosztowniejsze niż inne metody ze względu na zużycie ścierniwa i konieczność utrzymania wysokociśnieniowego sprzętu. Jednakże, jego wszechstronność, precyzja i zdolność do cięcia bez wpływu ciepła sprawiają, że jest to preferowana metoda w wielu zastosowaniach przemysłowych, od prototypowania po produkcję seryjną.
Podsumowanie
Każda z tych metod ma swoje miejsce w przemyśle, zależnie od wymagań dotyczących materiału, grubości, dokładności i kosztów. Cięcie strumieniem wody wyróżnia się swoją wszechstronnością i zdolnością do cięcia bez wpływu ciepła, co czyni je preferowaną metodą w wielu zastosowaniach.
Autor: inż. Włodzimierz Tadeusiak