Usługi CNC zwiększają produkcję seryjną na dużą skalę, oferując precyzję, wydajność i możliwości dostosowania w procesach produkcyjnych.
Spis treści:
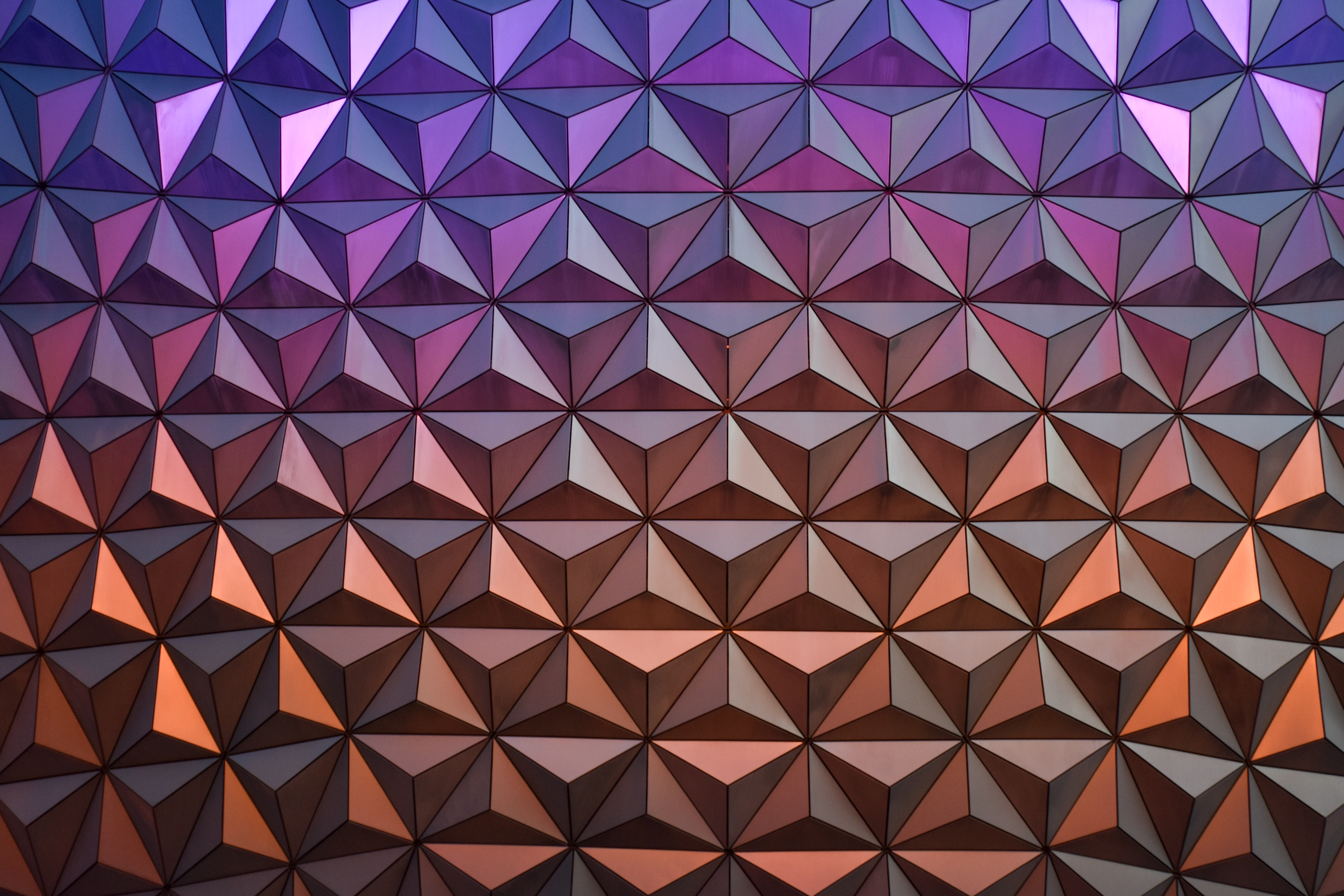
Jesteś zainteresowany usługą obróbki skrawaniem stali? Zapraszamy do kontaktu z naszą firmą. Oferujemy szeroki zakres usług w zakresie obróbki skrawaniem, wykorzystując najnowocześniejsze technologie i maszyny. Nasz zespół specjalistów gwarantuje najwyższą jakość wykonania, precyzję i efektywność w każdym projekcie.
MPT Components
Ul. Guido Henckela Donnersmarcka 15
41-807 Zabrze, woj. Śląskie
Najbliższe miasta Śląsk: Zabrze, Gliwice, Tarnowskie Góry, Bytom, Chorzów, Tarnowskie Góry, Ruda Śląska, Knurów, Katowice, Dąbrowa Górnicza
Zagłębianie się w obróbkę skrawaniem
Obróbka skrawaniem sterowana numerycznie stanowi filary nowoczesnego przemysłu wytwórczego, wyróżniając się precyzyjnością, efektywnością i elastycznością. Wykorzystują one komputerowe systemy sterowania oraz maszyny skrawające do precyzyjnego usuwania materiału z obrabianego elementu, co sprawia, że są one niezastąpione w tworzeniu skomplikowanych części z wysoką dokładnością.
Podstawy procesów obróbki skrawaniem i tokarstwa CNC
Frezowanie CNC i toczenie metalu to proces, w którym przedmiot jest mocowany, a sterowane komputerowo narzędzie tnące uszeregowane w wielu punktach przekształca materiał. Frezarki mogą obracać się w różnych płaszczyznach, tworząc rozmaite formy, rowki, otwory i szczegóły w materiałach takich jak metal, tworzywa sztuczne czy drewno. Wielofunkcyjność frezarek CNC, w tym popularnych modeli 3-osiowych, 4-osiowych, a nawet 5-osiowych, umożliwia wykonanie skomplikowanych i dokładnych cięć, idealnie nadających się do produkcji złożonych lub unikatowych części.
Tokarstwo CNC, z kolei, polega na obracaniu obrabianego przedmiotu wokół narzędzia tnącego. Technika ta jest głównie stosowana do wytwarzania elementów o kształcie cylindrycznym, gdzie narzędzie tnące przesuwa się wzdłuż linii prostej. Tokarki, maszyny używane do tokarstwa, mogą mieć konstrukcję poziomą lub pionową, w zależności od wymagań co do osi obrabianego elementu.
Dokładność i efektywność w masowej produkcji
Dokładność jest charakterystyczną cechą obróbki CNC, przy czym nowoczesne frezarki i tokarki osiągają tolerancje tak małe jak ± 0,001 cala (± 0,0254 mm), co jest kluczowe dla sektorów wymagających wysokiej precyzji, takich jak przemysł lotniczy czy medyczny. Efektywność jest równie istotna; standardowe maszyny CNC mogą działać bez przerwy przez długi czas, często 24 godziny na dobę, 7 dni w tygodniu, z minimalnym nadzorem, znacząco redukując czas produkcji i koszty pracy.
- Analiza kosztów: Mimo że początkowe wydatki na maszyny CNC mogą być wysokie, zwiększenie szybkości produkcji, efektywności i precyzji z czasem znacznie zniża te koszty. Na przykład średniej klasy frezarka CNC może kosztować od $ 50 000 do $ 150 000, ale obniżenie nakładu pracy fizycznej i zdolność do ciągłego wytwarzania części zapewniają szybki zwrot z inwestycji.
- Wszechstronność w doborze materiałów: Maszyny CNC mogą obrabiać szeroką gamę materiałów. Metale, takie jak aluminium i tytan, tworzywa sztuczne, na przykład ABS i PEEK, a także kompozyty, mogą być obrabiane z wysoką precyzją, co sprawia, że technologia CNC jest wszechstronnym rozwiązaniem dla wielu sektorów.
- Prędkość i jakość: Nowoczesne maszyny CNC działają z wysoką prędkością, z prędkościami wrzeciona dochodzącymi do 25 000 obr./min, co skraca czas cyklu i zwiększa produktywność. Jakość wytworzonych części CNC jest stale wysoka, minimalizując odpady i zapotrzebowanie na naprawy czy korekty po produkcji.
Pomimo wielu zalet, niezmiernie istotne jest rozpoznanie pewnych ograniczeń i wyzwań. Na przykład złożoność projektów może wydłużyć czas potrzebny na programowanie i wymagać zaawansowanych narzędzi, potencjalnie zwiększając całkowity koszt. Jednak w kontekście masowej produkcji, efektywność, dokładność i powtarzalność obróbki skrawaniem i tokarstwa CNC często przewyższają te wyzwania, czyniąc je niezbędnymi w obecnym środowisku produkcyjnym.
Produkcja seryjna w obróbce skrawaniem
Wdrażanie usług CNC w seryjnych procesach produkcyjnych jest strategicznym krokiem, który może znacząco poprawić efektywność produkcji, jakość wyrobów i opłacalność. Efektywna strategia integracji uwzględnia specyficzne wymagania produkcyjne i maksymalizuje wykorzystanie możliwości CNC, aby zaspokoić te potrzeby.
Ocena wymagań produkcyjnych i możliwości CNC
Przed wdrożeniem usług CNC, niezbędna jest szczegółowa ocena potrzeb produkcyjnych oraz możliwości oferowanych przez maszyny CNC. Obejmuje to analizę:
- Poziomu produkcji: Określenie ilości wymaganych części w określonym czasie. Maszyny CNC są optymalne do produkcji w średniej i dużej skali, ale wybór konkretnego modelu i ilości maszyn zależy od przewidywanej wydajności.
- Złożoności elementów: Określenie złożoności wytwarzanych elementów. Bardziej skomplikowane części z wąskimi tolerancjami mogą wymagać zaawansowanych maszyn CNC, co wiąże się z wyższymi kosztami. Na przykład, maszyna CNC 5-osiowa może kosztować od 200 000 do ponad 500 000 dolarów, jednak umożliwia ona produkcję skomplikowanych części z wysoką dokładnością.
- Wymagania materiałowe: Identyfikacja używanych materiałów i ich zgodności z obróbką CNC. Koszt materiałów może się znacznie różnić, na przykład obróbka tytanu lub specjalnych stopów może być kosztowniejsza ze względu na cenę materiału i obciążenie, jakie wywierają na maszyny.
- Analizę kosztów i korzyści: Rozważenie początkowych kosztów instalacji, w tym zakupu maszyn CNC, oraz bieżących wydatków takich jak utrzymanie, narzędzia i robocizna. Maszyna CNC średniej klasy może być eksploatowana przez 10-15 lat, zapewniając długoterminową rentowność inwestycji.
Optymalizacja przepływu pracy i procesów integracji
Wprowadzenie usług CNC do linii produkcyjnych wymaga więcej niż tylko instalacji sprzętu. Potrzebne jest strategiczne planowanie przepływu pracy i optymalizacji procesu, obejmujące:
- Optymalizację procesów: Analizę całego procesu produkcyjnego od surowca do gotowego produktu. Należy zidentyfikować etapy, gdzie obróbka CNC może zastąpić lub wspierać istniejące procesy, skracając czas cyklu i poprawiając wydajność. Na przykład, integracja zautomatyzowanych maszyn CNC może redukować czas realizacji zadania z godzin do minut.
- Planowanie przepływu pracy: Projektowanie przepływu pracy, aby zminimalizować czas przestojów i zapewnić płynne przejście pomiędzy etapami produkcji. Może to wymagać reorganizacji przestrzeni produkcyjnej, aby ułatwić logiczny przepływ materiałów oraz integrację maszyn CNC z innymi systemami zautomatyzowanymi.
- Integracja kontroli jakości: Wprowadzenie kontroli jakości w procesie obróbki CNC. Nowoczesne maszyny CNC mogą oferować systemy monitorowania w czasie rzeczywistym, które kontrolują i dostosowują odchylenia, zapewniając, że każda część spełnia wysokie wymagania dokładności.
- Szkolenie i zaangażowanie pracowników: Zapewnienie, że personel jest odpowiednio przeszkolony w obsłudze, utrzymaniu i rozwiązywaniu problemów związanych z maszynami CNC. Kwalifikowani operatorzy mogą znacznie zwiększyć wydajność oraz trwałość maszyn CNC, maksymalizując zyski z inwestycji.
Dobór maszyn do seryjnej produkcji
Dopasowanie odpowiedniego sprzętu i technologii CNC do produkcji seryjnej jest niezbędne do skutecznego rozszerzania zakresu produkcji. Odpowiednia konfiguracja musi uwzględniać równowagę między kosztami, precyzją, szybkością oraz trwałością, aby odpowiadała na specyficzne wymagania produkcji na dużą skalę.
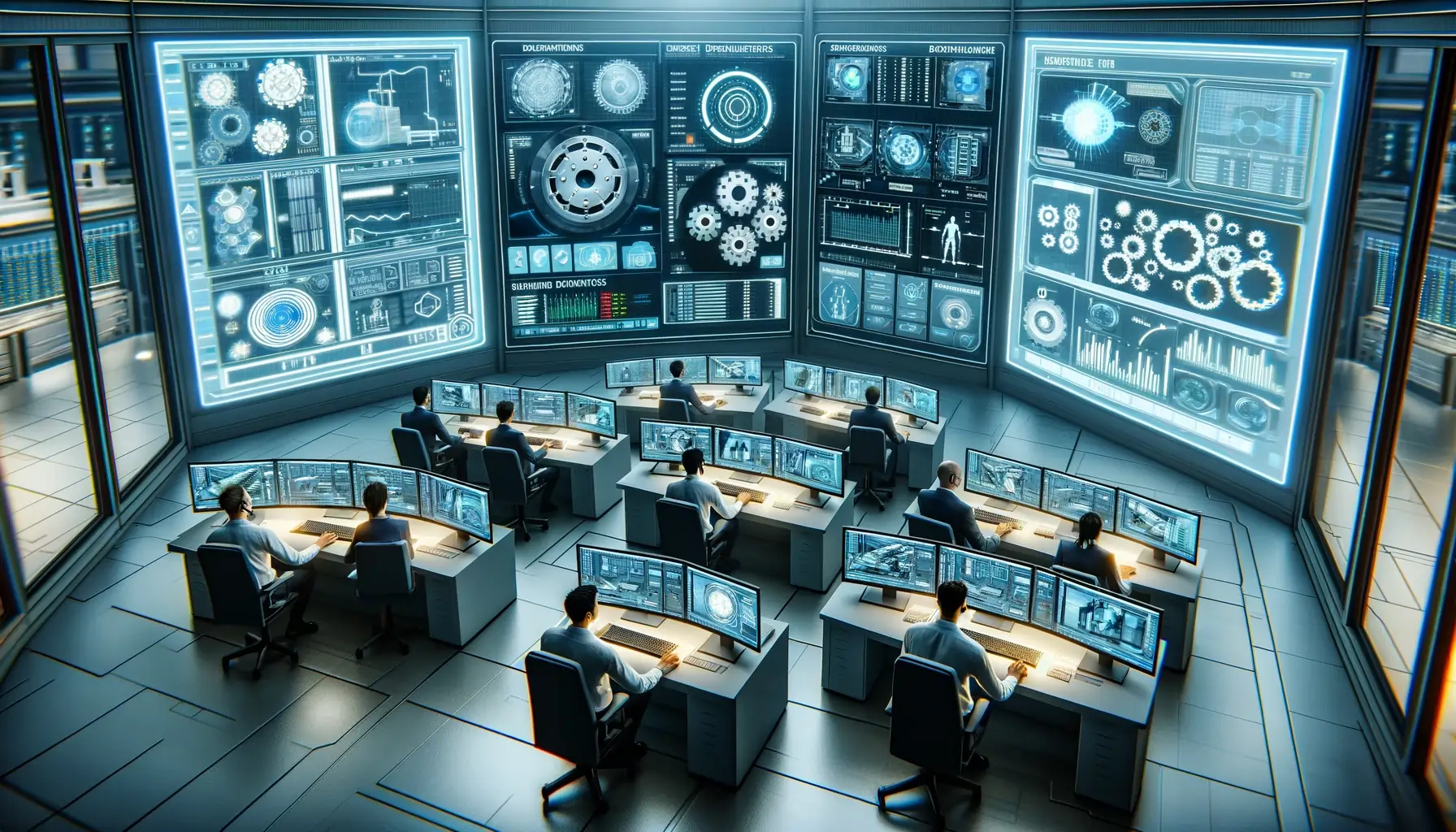
Ocena wyboru sprzętu CNC dla produkcji masowej
Podczas wybierania sprzętu CNC na potrzeby masowej produkcji, istotne jest zwrócenie uwagi na kilka kluczowych aspektów:
- Typ i wielkość maszyny: Wybór odpowiedniego rodzaju maszyny (frezarki, tokarki, czy urządzenia wielofunkcyjne) oraz jej rozmiaru powinien być podyktowany wymiarami i złożonością obrabianych części. Większe maszyny mogą oferować szerszy zakres możliwości, jednak zajmują więcej przestrzeni i zużywają więcej energii.
- Prędkość i moc wrzeciona: Wysokie prędkości obracania wrzeciona oraz duża moc są preferowane dla szybkiego usuwania materiału. Maszyny o prędkości wrzeciona wynoszącej 20 000 obr./min i mocy 25 kW mogą znacząco skracać czas cyklu obróbki dla określonych materiałów.
- Pojemność magazynka narzędziowego i szybkość zmiany narzędzia: Maszyny z większym magazynkiem narzędziowym i szybką zmianą narzędzi zwiększają wydajność przez redukcję czasu przestoju. Dla masowej produkcji idealna jest maszyna z automatycznym magazynkiem narzędzi (ATC) posiadającym 30 lub więcej narzędzi.
- Konfiguracja osi: Większa liczba osi zapewnia większą elastyczność i umożliwia produkcję skomplikowanych części. Maszyna 5-osiowa może być droższa w zakupie, ale może zredukować potrzebę wielokrotnej konfiguracji, oszczędzając czas i zwiększając precyzję.
- Precyzja i tolerancja: Należy ocenić zdolność maszyny do utrzymania ścisłych tolerancji, co jest krytyczne w branżach o wysokich wymaganiach precyzyjnych. Maszyny CNC zapewniające tolerancje rzędu ± 0,0005 cala mogą być niezbędne dla niektórych zastosowań.
Rozważania dodatkowe
- Kompatybilność materiałowa: Upewnij się, że maszyna jest przystosowana do obróbki wybranych materiałów, od metali po tworzywa sztuczne i kompozyty.
- Trwałość i konserwacja: Zastanów się nad żywotnością maszyny i dostępnością wsparcia od producenta dotyczącego konserwacji i części zamiennych.
- Analiza kosztów: W analizie kosztów należy uwzględnić nie tylko cenę zakupu maszyny, ale również koszty instalacji, eksploatacji, konserwacji oraz potencjalne przestoje.
Dokonując wyboru sprzętu i technologii CNC, ważne jest, aby nie kierować się wyłącznie ceną zakupu, lecz rozważyć wszystkie czynniki wpływające na wydajność produkcji i całkowity koszt posiadania. Wybór maszyn, które są dopasowane do specyfik produkcji i zapewniają wysoką wydajność, może znacząco zwiększyć opłacalność i konkurencyjność przedsiębiorstwa na rynku.
Zaawansowane technologie zwiększające efektywność produkcji seryjnej
Implementacja nowoczesnych technologii w operacjach CNC może znacząco zwiększyć wydajność produkcji masowej, oferując jednocześnie spójność jakościową i zmniejszając koszty operacyjne.
Automatyzacja i Robotyka
- Integracja z robotycznymi systemami załadunku i rozładunku może drastycznie ograniczyć potrzebę interwencji człowieka, co przekłada się na szybszy przebieg produkcji. Systemy te mogą działać bez przerwy, zapewniając ciągłość procesów produkcyjnych nawet poza standardowymi godzinami pracy.
Monitorowanie i Kontrola w Czasie Rzeczywistym
- Zastosowanie systemów monitorujących takie jak sensory zużycia narzędzi, obciążenia oraz temperatury w czasie rzeczywistym umożliwia wykrywanie i zapobieganie problemom jeszcze zanim te wpłyną negatywnie na produkcję. Dzięki temu możliwe jest utrzymanie wysokiej jakości wytworzonych części oraz minimalizacja czasu przestoju maszyn.
Oprogramowanie do Symulacji i Optymalizacji
- Zaawansowane oprogramowanie CAD/CAM pozwala na precyzyjne symulowanie procesów obróbczych, co umożliwia identyfikację i eliminację potencjalnych problemów przed rozpoczęciem faktycznej produkcji. Optymalizacja ścieżek narzędzi i strategii skrawania przyczynia się do maksymalizacji efektywności i dokładności produkcji.
Korzyści Wynikające z Zaawansowanych Technologii
- Zwiększona wydajność produkcji: Automatyzacja, w połączeniu z ciągłym monitorowaniem i optymalizacją procesów, pozwala na zauważalne zwiększenie tempa produkcji, co jest kluczowe w przypadku dużych wolumenów.
- Spójna jakość: Stosowanie systemów monitorowania w czasie rzeczywistym i zaawansowanych technik kontroli jakości zapewnia wysoką jednorodność i jakość produkowanych części, co jest niezwykle ważne w branżach o wysokich wymaganiach tolerancyjnych.
- Zmniejszone koszty pracy: Implementacja robotów i automatyzacji procesów zmniejsza zapotrzebowanie na pracę ręczną, szczególnie w zadaniach wymagających dużej precyzji i powtarzalności, co przekłada się na obniżenie kosztów operacyjnych.
Integracja zaawansowanych technologii w procesach CNC umożliwia przedsiębiorstwom nie tylko zwiększenie wydajności i jakości, ale także zaoferowanie bardziej konkurencyjnych cen dzięki zmniejszeniu kosztów produkcji. W dzisiejszym dynamicznym środowisku rynkowym, inwestycja w nowoczesne rozwiązania technologiczne jest kluczowa dla utrzymania przewagi konkurencyjnej i zaspokojenia rosnących oczekiwań klientów.
Zarządzanie siłą roboczą w produkcji seryjnej
Zarządzanie dynamiką siły roboczej i skuteczne programy szkoleniowe są kluczowymi czynnikami w optymalizacji operacji CNC. Zaangażowany i wysoko wykwalifikowany zespół nie tylko zwiększa produktywność, ale także wprowadza innowacje i poprawia jakość w procesach obróbki CNC. Poniżej omówiono kluczowe aspekty budowania i rozwijania takiego zespołu.
Wymagania dotyczące umiejętności operatorów maszyn CNC
- Biegłość techniczna: Operatorzy muszą posiadać głęboką wiedzę na temat działania maszyn CNC, w tym zrozumienie prędkości wrzeciona, prędkości posuwu, oraz wybór odpowiedniego oprzyrządowania do obrabianych materiałów.
- Umiejętności komputerowe: Znajomość oprogramowania CAD/CAM jest niezbędna do efektywnego projektowania procesów obróbki oraz symulacji.
- Uwaga na szczegóły: Dokładność i precyzja są niezbędne, aby zagwarantować, że wyprodukowane części spełniają wymagane specyfikacje.
- Umiejętności rozwiązywania problemów: Operatorzy muszą być zdolni do szybkiego identyfikowania i rozwiązywania problemów związanych z maszynami lub procesami obróbki.
Programy szkoleniowe
- Szkolenie w miejscu pracy: Bezpośrednia praktyka pod okiem doświadczonych mentorów jest niezastąpiona. Pozwala na zdobycie praktycznych umiejętności i bezpośrednie stosowanie teorii w rzeczywistych warunkach pracy.
- Formalne programy edukacyjne: Programy oferowane przez szkoły techniczne i zawodowe zapewniają solidne fundamenty teoretyczne oraz umożliwiają praktyczne ćwiczenia na maszynach CNC.
- Szkolenie producentów maszyn: Specjalistyczne szkolenia oferowane przez producentów maszyn CNC mogą dostarczyć szczegółowych informacji o konkretnych modelach maszyn, z których operatorzy będą korzystać.
Uwagi dotyczące organizacji szkolenia
- Budżetowanie na szkolenia: Jest kluczowe dla zapewnienia ciągłego rozwoju umiejętności pracowników. Inwestycja w szkolenie przekłada się na wyższą jakość pracy, mniejszą liczbę błędów i wydajniejsze wykorzystanie sprzętu.
- Alokacja czasu: Należy przewidzieć regularne szkolenia i rozwój umiejętności pracowników. Choć może to oznaczać krótkoterminowe zmniejszenie produkcji, długofalowe korzyści w postaci poprawy efektywności i jakości są nieocenione.
Stworzenie kultury ciągłego uczenia się i rozwoju w zespole CNC jest fundamentalne dla utrzymania konkurencyjności i innowacyjności w dynamicznie zmieniającym się środowisku technologicznym. Angażowanie pracowników w procesy decyzyjne i dawanie im możliwości rozwoju podnosi morale i lojalność, co przekłada się na lepsze wyniki operacyjne.
Analiza kosztów i budżetowanie produkcji seryjnej
Sukces wdrożenia technologii CNC w procesach produkcyjnych wymaga dokładnego zrozumienia i zaplanowania zarówno bezpośrednich, jak i pośrednich kosztów związanych z tą inwestycją. Odpowiednie budżetowanie i analiza kosztów są niezbędne, aby zapewnić, że integracja CNC przyniesie oczekiwane korzyści finansowe. Oto główne elementy, które należy uwzględnić w analizie kosztów i budżetowaniu:
Koszty początkowe
- Zakup maszyn CNC: Koszty zakupu mogą znacznie różnić się w zależności od specyfikacji i możliwości maszyny. Zaawansowane maszyny 5-osiowe są droższe, ale oferują większą elastyczność i potencjał produkcyjny niż prostsze maszyny 3-osiowe.
- Instalacja i konfiguracja: Obejmuje nie tylko fizyczny montaż maszyny, ale również jej kalibrację i pierwsze uruchomienie. Koszty te mogą się zwiększyć w zależności od potrzeb infrastrukturalnych, takich jak podstawy, instalacje elektryczne czy systemy odprowadzania wiórów.
Koszty operacyjne
- Materiały: Cena surowców jest kluczowym czynnikiem kosztowym i może wahać się w zależności od rodzaju materiału oraz fluktuacji cen na rynkach światowych.
- Energia: Koszt energii jest ważnym czynnikiem kosztowym, szczególnie w przypadku intensywnego użytkowania maszyn CNC, które mogą mieć duży wpływ na zużycie energii w zakładzie produkcyjnym.
- Konserwacja i naprawy: Budżet na konserwację i naprawy jest niezbędny do utrzymania maszyn w dobrym stanie technicznym i zapewnienia ich długotrwałej efektywności.
Dodatkowe aspekty budżetowania
- Szkolenia dla pracowników: Inwestycje w szkolenia są kluczowe dla zapewnienia, że personel jest w pełni przygotowany do efektywnego wykorzystania maszyn CNC.
- Oprogramowanie: Koszty zakupu lub subskrypcji oprogramowania CAD/CAM oraz potencjalnych aktualizacji, które są niezbędne do projektowania i programowania ścieżek narzędzi.
- Zużycie narzędzi: Narzędzia skrawające i inne komponenty zużywają się w procesie produkcji, co wymaga regularnej wymiany.
Przygotowanie kompleksowego budżetu wymaga uwzględnienia wszystkich powyższych aspektów, aby zapewnić, że inwestycja w CNC przyniesie oczekiwane korzyści. Kluczem do sukcesu jest również stała analiza i optymalizacja kosztów operacyjnych oraz adaptacja do zmieniających się warunków rynkowych i technologicznych, co może zapewnić trwałą konkurencyjność i rentowność wdrażanych rozwiązań CNC.
Wniosek
Produkcja seryjna w obróbce skrawaniem odgrywa kluczową rolę w nowoczesnym przemyśle wytwórczym, umożliwiając masową produkcję części i komponentów z wysoką precyzją i spójnością. Dzięki zaawansowanym technologiom CNC (Computer Numerical Control), przedsiębiorstwa są w stanie szybko i efektywnie przetwarzać szeroką gamę materiałów, od metali po tworzywa sztuczne, dostosowując się do zmieniających się wymagań rynkowych i potrzeb klientów. Kluczowe aspekty, takie jak wybór odpowiedniego sprzętu, optymalizacja procesów produkcyjnych, zarządzanie jakością, oraz inwestycje w szkolenie personelu, są niezbędne do maksymalizacji efektywności i rentowności produkcji seryjnej. W miarę postępu technologicznego i rosnącej konkurencji, ciągłe doskonalenie metod i procesów produkcyjnych będzie miało kluczowe znaczenie dla utrzymania przewagi konkurencyjnej na globalnym rynku.
Autor: inż. Włodzimierz Tadeusiak